十大线上配资 探访智能工厂:老师傅收了机器人当徒弟
人、工厂、智能装备、大市场……站在21世纪全球制造业创新发展的潮头十大线上配资,中国智能工厂从0到1、面向未来,正在寻求自己的答案。
有的企业进入行业赛道之初就走上了数字化之路;有的企业身处传统行业,与时俱进进行数字化改造;有的企业紧抓创新,加快智能制造步伐……上海证券报记者走进这些企业的智能工厂,寻找制造业高质量发展“密码”。
应时、应势、应需之举
宁德没有机场。从北京去宁德,只能先飞到福州,再转车1个小时,才能到达。
1个小时里,全球最大的动力电池制造商之一——宁德时代第一座“灯塔工厂”Z工厂,已经有3600个电芯下线。平均1秒产出1个电芯,这是世界顶级产速。
“灯塔工厂”被认为是当今全球制造业领域智能制造和数字化最高水平。目前,我国“灯塔工厂”数量居全球首位,“灯塔工厂”正不断丰富“智造”内涵,成为中国智能制造的示范样本。
何谓“智造”?为何“智造”?不同企业有着不同的见解。
——宁德时代说:“不用数字化装备,也可以制造电池,但产品质量和成本完全没有市场竞争力,这个道理非常简单。可以说,从建厂之初,我们就走上了智能制造之路。”
走在400米长的东湖工厂参观通道,宁德时代工作人员告诉记者,动力电池的现状,是高端产能不足、低端产能过剩。2012年宁德时代拿下宝马订单,成为公司在市场竞争中“脱颖而出”的关键一战。因为业内皆知,作为全球制造业标杆的宝马,对供应商筛选及产品品质的要求是极为严格的。而今,宁德时代早已占据国内动力电池装机量的半壁江山,全球市占率位居第一。
三一重工“灯塔工厂”组装的产品记者史丽摄
——三一重工说:“数字化转型,要么翻身,要么翻船。”
走进三一重工北京桩机工厂,制造车间的焊接线上,几台配备自动焊枪的机器人,正在焊接一根20多米长的钻杆。
三一重工重机事业部北京工艺院院长尹言虎对记者说,以前工厂的工作场景以手工为主,像摆地摊,生产一台旋挖钻机要1个月左右。以前有1000多名工人,年产值30多亿元。2019年,工厂开始进行数字化改造。现在生产一台旋挖钻机只要七八天,年产值最高达到70多亿元,人均产值超1000万元,一下子就尝到数字化的“甜头”。
——赛力斯汽车说:“只有坚持技术创新,才能为用户打造出极致体验、舒适便捷、可持续成长的产品和服务。这正是公司获得市场认可的‘秘诀’。”
赛力斯相关负责人向记者表示,作为拥有20年整车制造经验的企业,赛力斯汽车通过坚持创新驱动,实现了从传统生产到智能制造和质量自动化的跃迁,向新能源汽车产业转型升级。
何谓“智造”?又为何“智造”?不同企业也有着同样的注解:智能制造,是产品迭代升级的必然选择,也是市场竞争的迫切需要。
工业和信息化部数据显示,目前各地建设数字化车间和智能工厂近8000个。其中,2500余个基本完成数字化转型,209个成为具有国际先进水平的智能制造示范工厂。通过智能化改造,这些示范工厂产品研发周期平均缩短20.7%,生产效率平均提升34.8%。
借新技术、新应用“东风”而起
新技术、新装备、新应用,智能工厂的最大特征,恰是这些。
宁德时代智能工厂记者于祥明摄
走进宁德时代总部Z基地工厂,空无一人的生产车间里,中控系统有条不紊地向所有子设备传送工作指令,一台台搭载视觉传感器的机械臂灵活舞动,AGV自动运输车来回穿梭,高科技机器人自动检测电池缺陷……
“智能制造的核心是制造,要以工艺和装备为主。”宁德时代总裁助理吕鹏告诉记者,宁德时代建厂之初,国内不少工厂的核心装备都是从国外进口,“我们买不到最先进的,干脆从一开始就和国内机械制造企业一起研发国产智能装备。”
以涂布工序为例,为了确保产品良率,车间中安装了强大的“鹰眼系统”——8K高清摄像机,通过超低时延的5G网络,将涂布过程实时传输到机器视觉系统,任何微小缺陷都会被“鹰眼”系统识别。
为什么要上这套装备?相关专家告诉记者,这是因为高端动力锂电池制造工艺复杂,质量影响因素极多,缺乏智能管控技术,导致质量一致性差,生产效率低。而且,锂电池行业存在的这些制造问题,无法通过传统手段优化,也没有现成样本可以参照,只能通过应用智能制造的新技术、新理念,有针对性地解决行业难题。
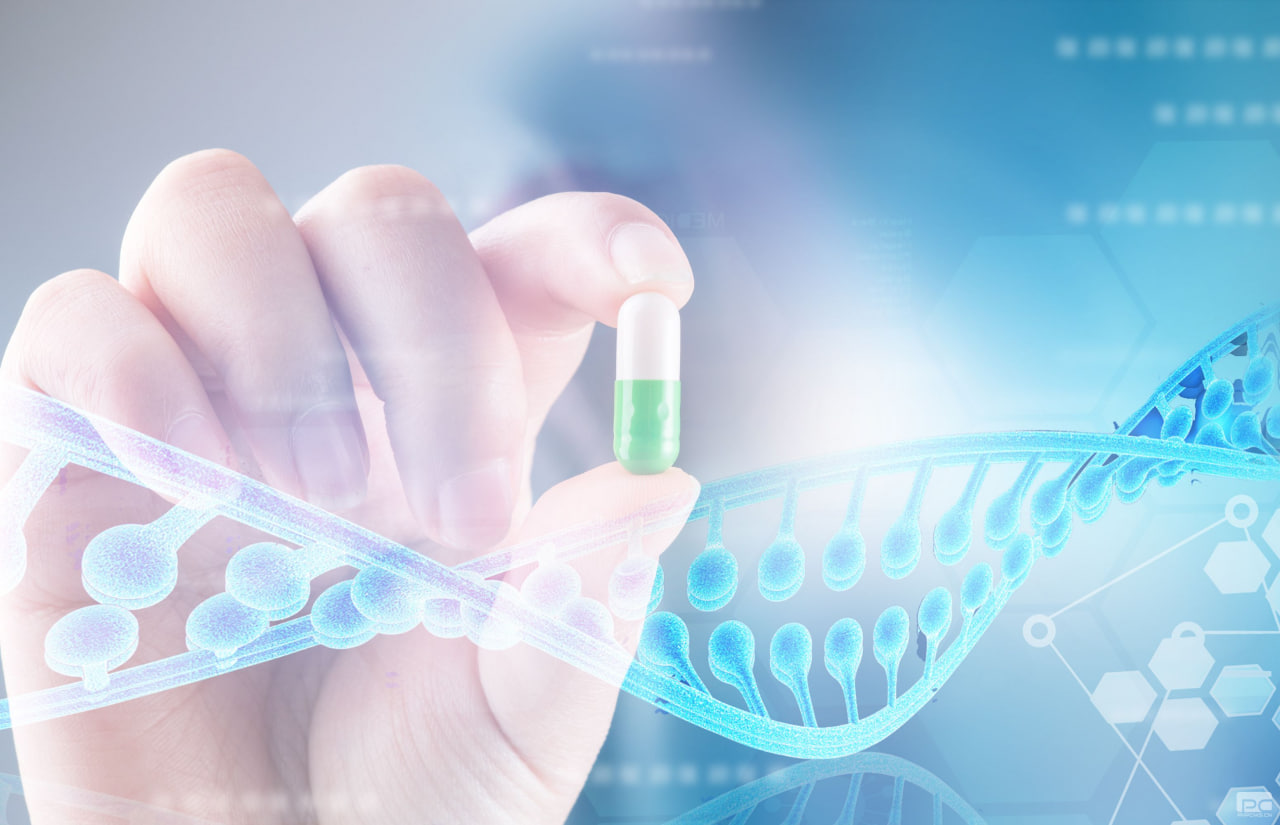
在调研中,记者了解到,5G技术成为不少智能工厂的“标配”。
“传统网络通信方式覆盖范围小、信号不稳定,难以满足智能应用需求。2019年北京桩机工厂率先部署5G网络基础设施,探索5G与工业互联网深度融合,将500台生产设备、传感器和600台水电油气工业仪表全部接入公司自研的‘根云’工业互联网平台,覆盖焊接、涂装等全部工艺,实现远程实时数据采集、设备控制、故障诊断等功能。”尹言虎告诉记者,与5G融合的新装备发挥了重要作用,三一重工北京桩机工厂共有8个柔性工作中心、16条智能化产线、375台全联网生产设备,可以实现从订单到交付的全流程数据驱动……
三一重工“灯塔工厂”制造的桩机记者史丽摄
同样,赛力斯相关人士告诉记者,工厂有超过1000台机器人协同运作,关键工序100%自动化生产。在整车下线后,通过全身“CT扫描”,对整车400多项功能进行自动化测试,测试数据实时上云,实现“一车一体检报告”,保证出厂的每一台车都100%合格,而且全程自动化。
“通过工业互联网、大数据、人工智能与实体制造相融合,我们在机器决策、物流自动化、生产少人化、机器视觉、自纠正算法、5G等方面开展了广泛应用。在生产效率和生产周期等方面提升了30%以上。”三一重机北京公司总经理左朝永告诉记者。
“我们认为智能制造应具备多个特征,其落地步骤为工艺创新、装备创新、数据互联、AI应用、5G联通等。”吕鹏说。
“大数据、云计算、人工智能等新一代信息技术快速发展,推动制造业向数字化、网络化、智能化迈进,带来历史性机遇。”中国工程院战略咨询中心制造业研究室副主任臧冀原认为,全球制造业竞争格局正在重塑,智能制造装备、软件和系统集成是制造业转型升级的关键支撑。
人才是最关键因素
是人更精巧,还是机器更好?对于这个问题,尹言虎没有直接回答,而是讲了一个故事。
“我们原来有一道焊接工序,就一位老工人能干这个活儿,他若有事请假,就要歇工。后来工厂改造时引入自动化机器人,还找到参与过国家体育场‘鸟巢’建设的焊接专家进行指导,把相应的焊接经验参数化,编程到机器人里。电流电压到底是多少,怎么摆动,怎么焊接……我们把这些项目参数化之后,无论何时把这个机器人调出来,其焊接的产品都是合格的。”尹言虎说。
制造业数字化转型,并不能简单理解成“机器换人”。记者从调研中了解,智能工厂对工人、工程师也提出了新需求,老师傅们教会机器人“新徒弟”后,培训掌握机器人编程,走上给机器人下发指令的新岗位,师徒变成人机协同的“新搭档”。
例如,三一重工公司提出,三一未来加速推动数字化转型,目标是拥有30000名工程师、3000名产业工人,实现3000亿元销售额。人才结构的变化,意味着三一智能制造的发展原动力将从劳动力红利切换到工程师红利,与时代共振。
三一重工“灯塔工厂”的焊接机器人记者史丽摄
宁德时代对研发人才的需求十分巨大。记者在宁德时代总部餐厅看到,科技“白领”人头攒动。宁德时代2023年半年报披露,截至报告期末,公司拥有研发技术人员17998名。其中,拥有博士学历283名、硕士学历2972名。
“我们公司把技术创新作为最核心的竞争力。这不是一句口号,而是踏踏实实的行动、持之以恒的努力。”吕鹏向记者坦言,科技创新其实没有秘诀,最根本还是靠人才、靠研发堆出来的,要下苦功夫。
“毫无疑问,人才是智能工厂、智能制造中最关键的因素,各方应给予重视。”臧冀原向记者表示,到2027年我国智能制造将推动规上企业全面开展数字化转型,需要上百万人才。因此,《“十四五”智能制造发展规划》提出十大线上配资,强化人才培养,包括定期编制智能制造人才需求预测报告和紧缺人才需求目录,研究制定智能制造领域职业标准,优化学科专业和课程体系设置,加快高端人才培养,以及弘扬企业家精神和工匠精神,鼓励开展智能制造创新创业大赛、技能竞赛等。